In manufacturing, problems don’t just appear out of nowhere — they arise from a web of interrelated causes.
A machine breaks down. A product gets rejected. A delivery is delayed. It’s easy to jump into action and fix what’s immediately visible — but those quick fixes often treat only the symptoms. The real problem? Still lurking beneath the surface. That’s where Root Cause Analysis (RCA) comes in.
RCA isn’t about blame — it’s about understanding. It’s a structured approach to problem-solving that digs deep to uncover the true reason something went wrong. Once you know why a problem happened — really happened — you can prevent it from recurring.
What is Root Cause Analysis — and Why Is It Crucial?
In any manufacturing setup, problems are inevitable — a machine breaks down, a product gets rejected, or a delivery gets delayed. But what separates high-performing teams from the rest isn’t how fast they fix the issue… it’s how deeply they understand why it happened.
Root Cause Analysis (RCA) is the process of identifying the true underlying cause of a problem — not just the visible symptom. It’s a structured, disciplined approach that focuses on permanent solutions rather than temporary patches.
Why is RCA so important?
Most problems on the shop floor are not isolated events. They’re indicators of larger, systemic weaknesses — in processes, training, communication, or equipment.
Fixing what’s visible may get operations back on track for now, but if the underlying issue remains unaddressed, the problem will likely return. Often, it will create bigger disruptions the next time around.
For example:
A rejected part might be blamed on operator error. But an RCA might reveal deeper causes:
- The operator wasn’t trained adequately
- The SOPs were outdated
- The inspection equipment hadn’t been calibrated
What appears to be a simple mistake is often the result of system-level failure.
By uncovering and addressing the root cause, organizations prevent recurrence and drive continuous improvement.
What Happens Without RCA?
When RCA is skipped, teams tend to fall into a cycle of quick fixes and recurring issues. The same problems keep showing up across shifts and lines, draining time, energy, and resources.
The long-term consequences can be severe:
- Problems reappear, creating repeat downtime or defects
- Teams stay in reactive mode, constantly firefighting
- Product quality deteriorates gradually
- People feel blamed, leading to lower engagement and morale
- Valuable insights are lost, because no one asked “why?”
In regulated or safety-critical industries, the stakes are even higher — overlooking root causes can lead to compliance violations, costly recalls, or hazardous situations.
RCA breaks this cycle by helping teams understand problems at their source. It creates a culture of learning over blame, and systems thinking over siloed action. That shift is what makes it so powerful — and so essential.
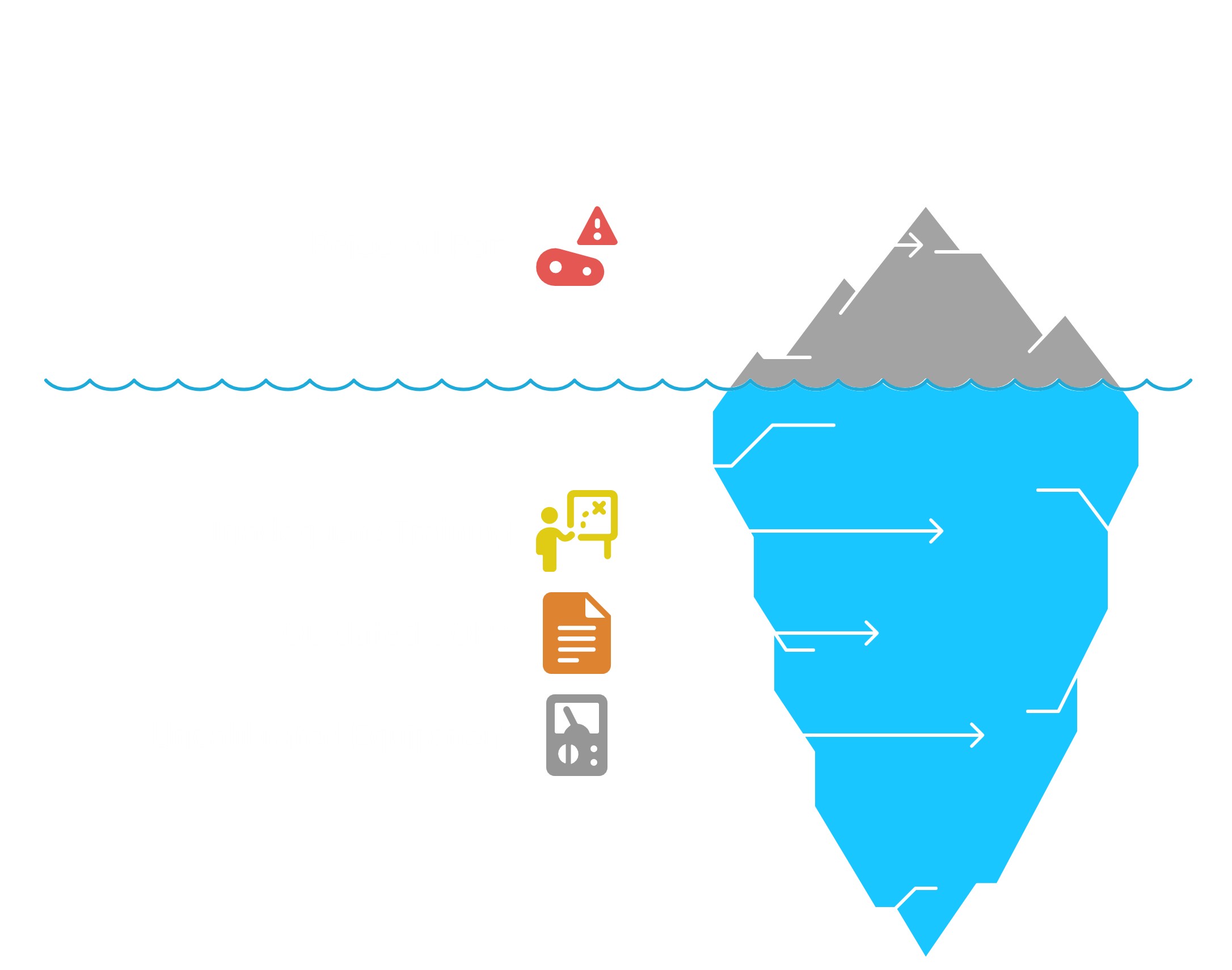
The Power of Asking “Why?” — Beyond the Surface
At the heart of Root Cause Analysis lies a deceptively simple yet powerful habit: asking “Why?” — again and again.
Popularized by Toyota’s Lean manufacturing philosophy, the 5 Whys technique is one of the most widely used tools in continuous improvement. The idea is straightforward: by asking “why?” five times in succession, teams can move past superficial symptoms and uncover the true cause of a problem.
The 5 Whys in Action
Let’s take a real-world example from the shop floor:
Problem: A batch fails the final quality inspection.
- Why? The part dimensions were out of tolerance.
- Why? The wrong fixture was used during machining.
- Why? The correct fixture was unavailable.
- Why? It was sent for repair but never replaced.
- Why? There’s no tracking or maintenance system for fixtures.
Root Cause: Lack of fixture management controls.
Instead of stopping at the immediate symptom — dimensional failure — the analysis uncovers a gap in asset tracking and preventive maintenance. This insight shifts the focus from blaming the operator to improving the system.
Why This Matters
The 5 Whys technique does more than solve problems. It drives a cultural shift — from blame to system thinking.
- It uncovers weaknesses in processes, not just people
- It reveals patterns that would otherwise go unnoticed
- It leads to solutions that are preventive, not just reactive
When teams adopt this mindset, small daily issues become opportunities to improve the way work gets done. Over time, this builds a foundation for operational excellence, consistency, and resilience.
RCA in Action: Tools, Techniques, and When to Use Them
Not every problem has the same shape — and not every root cause can be uncovered with the same method. The key to effective Root Cause Analysis is choosing the right tool for the complexity and context of the issue.
Here are four of the most commonly used RCA techniques, along with when and how to apply them:
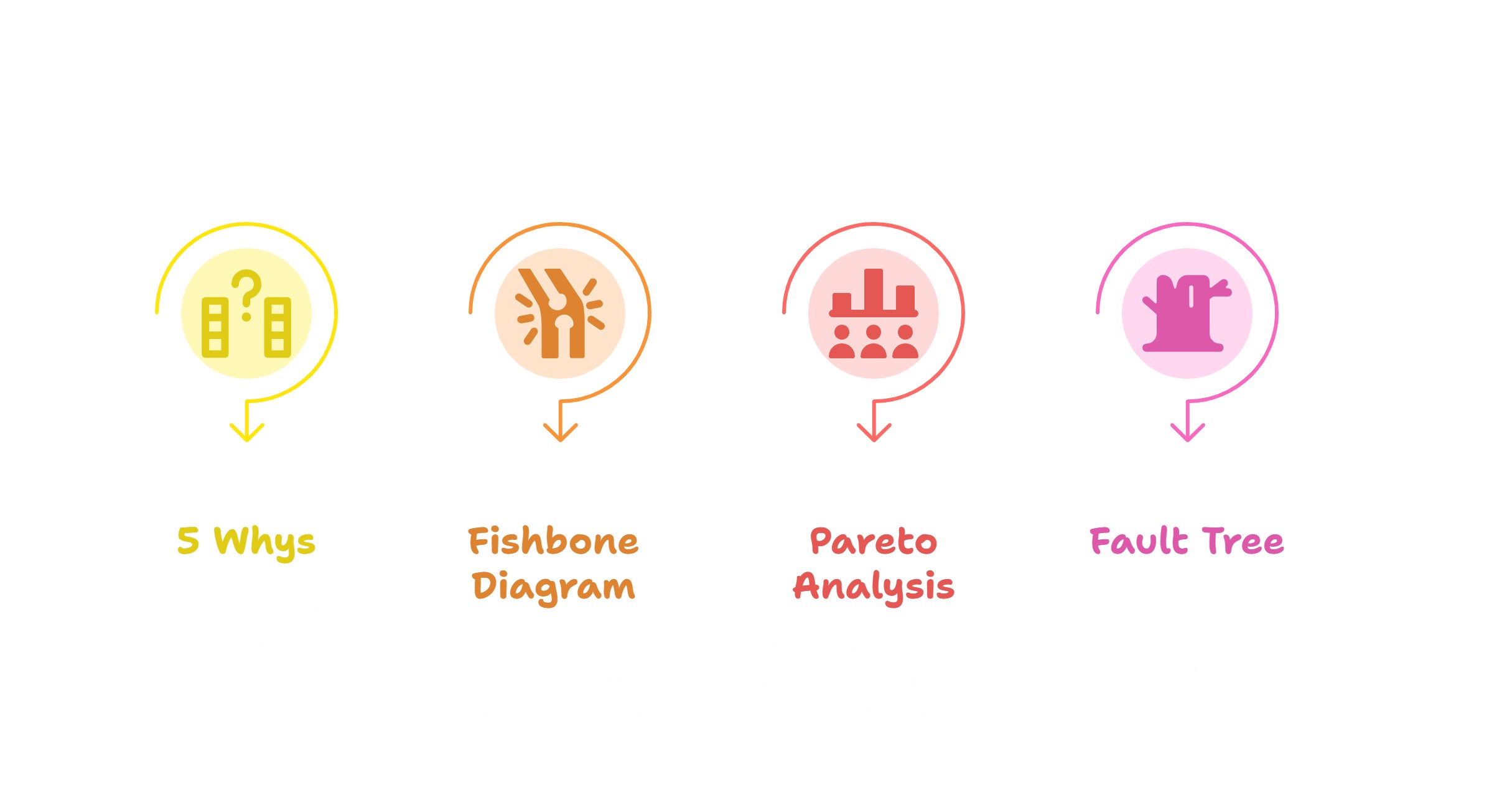
1. 5 Whys Analysis
Best for: Simple, linear problems with a single root cause
How it works: Ask “Why?” repeatedly (typically five times) until the core issue is uncovered.
When to use:
- Straightforward issues
- Operator or process-level problems
- Situations where quick problem-solving is needed
Example:
A delivery is delayed → Why? Maintenance overran schedule → Why? Schedule wasn’t updated → Why? Maintenance system isn’t integrated with production planning.
This tool is ideal for uncovering systemic process gaps hiding behind seemingly isolated events.
2. Fishbone Diagram (Ishikawa)
Best for: Complex, cross-functional problems with multiple contributing factors
How it works: Brainstorm causes across key categories like Man, Machine, Method, Material, Measurement, Environment — then drill deeper into each branch.
When to use:
- Quality issues spanning multiple teams
- Process variability across machines or lines
- Problems requiring collaborative input
Example:
Investigating high rejection rates across several production lines by exploring possible causes in process design, operator training, machine calibration, and raw material quality.
This technique visualizes cause-effect relationships, helping teams connect the dots and organize their investigation.
3. Pareto Analysis (80/20 Rule)
Best for: Prioritizing where to focus improvement efforts
How it works: Identify the “vital few” causes that contribute to the majority of problems (based on data).
When to use:
- When you have large volumes of data or defects
- To identify the most impactful problem areas
- To allocate resources effectively
Example:
Analyzing defect data and realizing that three recurring defects account for 80% of total rejections. Focus shifts to fixing those first.
Pareto Analysis supports data-driven decision-making, especially in quality management and continuous improvement initiatives.
4. Fault Tree Analysis (FTA)
Best for: High-risk, safety-critical, or regulated environments
How it works: Start with a top-level failure (e.g., system shutdown) and work backwards through logical branches of possible contributing events.
When to use:
- Complex equipment or systems with interdependencies
- Root cause investigations in industries like aerospace, medical devices, or energy
- Scenarios requiring formal risk mitigation documentation
Example:
Investigating equipment failure in a sterile packaging line where multiple sensors, processes, and components could have contributed.
FTA helps teams map out all possible failure paths and assess probability and impact — critical for compliance and risk assessment.
By selecting the right RCA method for the situation, manufacturers can uncover insights that lead to stronger processes, safer operations, and long-term resilience.
Final Thought: Fix Forward, Not Just Fix Fast
Root Cause Analysis is more than a tool — it’s a shift in mindset.
It encourages teams to move beyond quick fixes and start solving problems at their source. By digging deeper, RCA helps organizations learn from failure, improve systems, and prevent the same issues from recurring.
In today’s fast-paced, competitive, and highly regulated manufacturing environment, that approach isn’t just helpful — it’s essential.
When RCA is combined with the power of digital tools and real-time visibility, it becomes a cornerstone of:
- Continuous improvement
- Quality assurance
- Operational agility
Ultimately, the goal isn’t just to fix what’s broken — it’s to build systems that don’t break the same way twice.
Fixing forward means solving today’s problems in a way that strengthens tomorrow’s performance.
That’s the power of Root Cause Analysis.